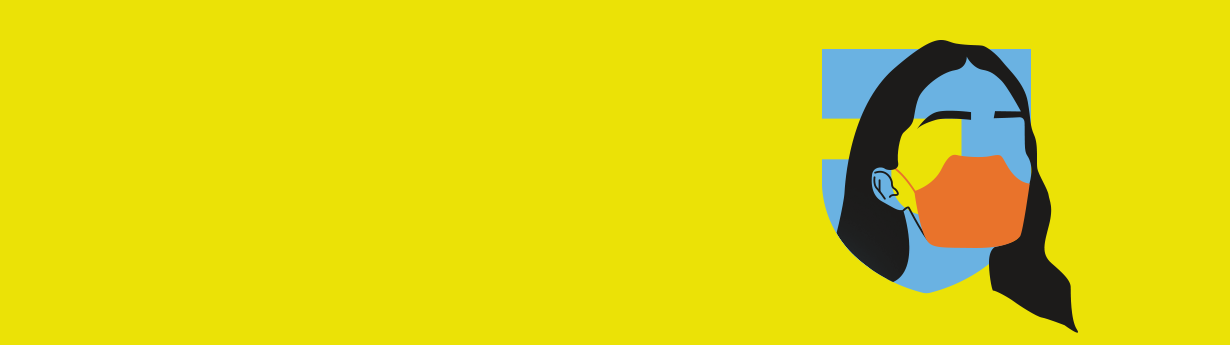
Textile Professionals Answer a Looming Need
By Cindy Lefler
11.09.20
Jefferson graduates keep businesses open to manufacture PPE
As graduate students at the Philadelphia College of Textiles and Science (now Thomas Jefferson University), Joy McGruther Alaoui and Taya Thongyoo Haught were used to being tasked with solving complex problems.
“We would run back and forth from the studio to the looms, then back to our computers, adjusting technical aspects—problem solving on the spot,” says Alaoui, who along with Haught runs The Weave Lab in Jessup, Pennsylvania. The challenges they met in the classroom trained the business partners to thrive in the professional world—but they never thought they would have to use those skills to survive a pandemic.
For Alaoui and Haught, as well as two other graduates-turned-business owners, the COVID-19 crisis could have spelled disaster—lost commerce, massive layoffs, financial ruin. Instead, they used their education and ingenuity to keep their companies running and their employees working, all while supplying much-needed essential supplies to hospitals, businesses, and individual citizens.
“When the pandemic hit and most furniture retailers closed, we needed to find something we could produce. So we started developing and manufacturing some PPE (personal protective equipment) products to keep our operations running,” says Iv Culp, president and CEO of Culp Incorporated, a manufacturer of mattress and upholstery fabrics headquartered in High Point, North Carolina.
Culp, who earned an MBA and master’s degree in textile marketing in 1998, transformed his facilities into producers of face masks and hospital bed covers almost overnight. He said the initiative to reprioritize operations to produce PPE wasn’t as much about profit as it was to keep as many workers as possible employed and support the country in a difficult time.
Bob Berger, president and CEO of the Ontario-based MW Canada, which manufactures textiles for the window fashion market, healthcare products, and air and water filtration systems, says he also knew when the pandemic arose he would have to adapt in order to survive and save jobs. As regular orders dwindled, he began researching the American Society for Testing and Materials (ASTM) requirements for PPE products.
“We tweaked the samples a little bit, started developing fabrics that would fit the existing machine setups, then waited for certification,” says Berger, who graduated in 1977 with a degree in textile engineering. Once the products were approved, the company started manufacturing fabric for hospital gowns, shipping about 20,000 yards of fabric a week to companies that sew the garments.
In less than a week we went from designing paisleys and polka dots to designing PPE.
Not only was he able to hire back all 100 employees he initially laid off at the start of the pandemic, but he also is now looking to hire more people to handle the workload created by the PPE demand, as well as the regular work, which has returned to normal.
“We looked at the PPE as a filler until regular business came back, but I think these products are going to be around for years to come,” Berger says, adding that as long as there is a demand, they will meet it as well as expand by developing new products. His company is now manufacturing ear loops for medical masks.
Non-medical-grade face masks have been the most in-demand product by far during the crisis.
Culp estimates that in the first three months of the pandemic, his company produced more than a million masks to sell to local businesses seeking to reopen safely and to donate to social organizations and school systems. While the masks are not medical-grade, they are designed to be FEMA approved for the average consumer so that medical grade mask supplies are available to healthcare workers.
At the onset of COVID-19, Alaoui, who earned a master’s degree in textile design with a concentration in weaving in 1998, and Haught, who received her master’s in 2001 in textile design with a focus on weaving, were working for Material Technology and Logistics (MTL), a weaver of specialty apparel and home furnishing fabrics. About 18 months ago, the pair started The Weave Lab, which is associated with MTL and concentrates on zero waste manufacturing by taking leftover bits of yarn that accumulate in weaving mills and turning them into small-batch, one-of-a-kind textiles.
As the call for masks started to surge, the pair was tasked with designing masks for MTL to make and donate to local hospital systems and assisted living and rehabilitation facilities in the Scranton area. Shortly afterward, they began fielding calls from their own customers at The Weave Lab asking about masks.
The two combined their zero-waste manufacturing techniques with a little creativity and came up with a high-end, aesthetically pretty no-sew mask kit. “The product itself could come straight off the loom and—with a few cuts and some laces—be ready to use,” says Alaoui.
“We researched particle penetration, fit, breathability, comfort, absorbency, filtration … all of the important aspects,” she says. “In less than a week, we went from designing paisleys and polka dots to designing PPE.”
All four Jefferson alumni predict that the need for PPE—particularly face masks—will be around for a long time, and as long as there is a need, the textile industry will be there to help.
“The textile industry is made up of a lot of great companies. It’s amazing to see how fast it rallied the troops and really made a huge difference in the PPE effort,” Culp says. “As long as we can help the cause and make products to help us recover from the crisis, we’ll keep doing it.”